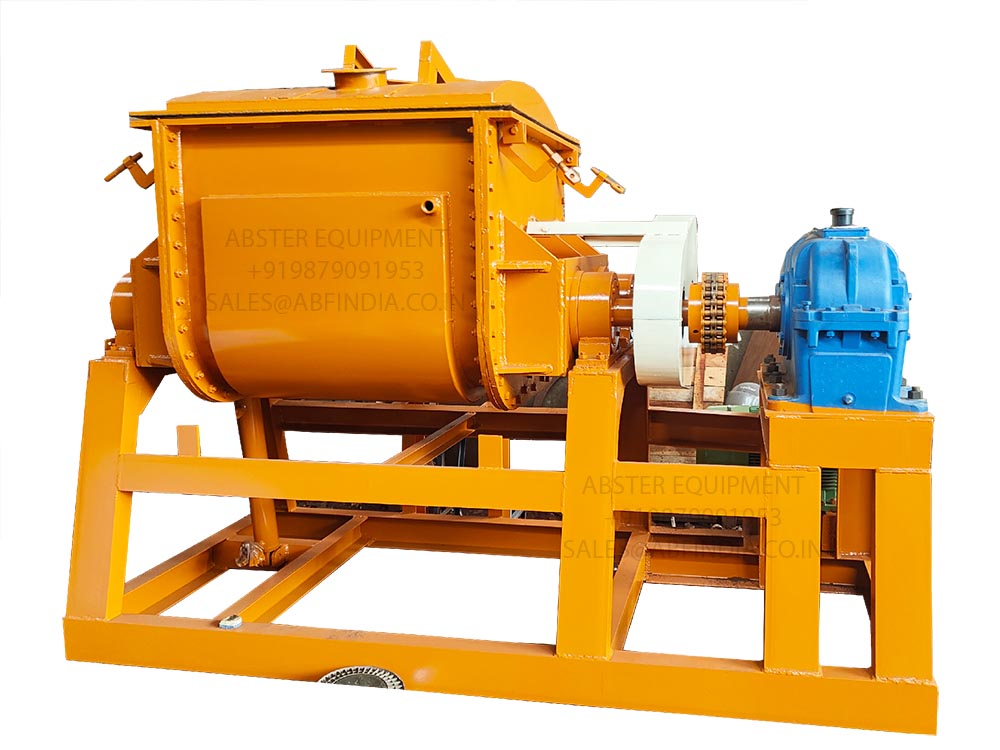
The CMC Sigma Mixer uses two Sigma-shaped paddles with different rotation speeds to produce strong shearing, squeezing and stirring to make the viscous materials mix quickly and evenly.
The Sigma blade mixer can be made into ordinary type, pressure type, vacuum box type, etc. The sigma mixer with vacuum box balance structure is unique design of our company …
The temperature adjustment form of the kneader adopts heat transfer oil heating, steam, water cooling and other methods.The output methods of the kneader include hydraulic cylinder tilting, bottom ball valve discharge, screw extrusion, etc.
CMC full name is Carboxy Methyl Cellulose which is an sticky material can be used on making different emulsified solution on different industries ,CMC is soluble is water ,so the material is with different viscosity and duo to its widely use on different production So the CMC production is normally high capacity and continuously .
There should have jacket for control the temperature for CMC materials ,heating and cooling jacket.
About Carboxymethyl Cellulose Sigma Mixer
sigma kneader mixer
Types of CMC sigma mixer
A combination of intense kneading, mixing, and shearing of kneader mixer equipment is used to process sticky, viscous, and dough-like materials. A typical Cellulose Sigma Mixer consists of twin branches grinders that rotate slowly. These grinders have an arc-shaped lining chamber inside which the materials are processed. Heat is generated by the friction produced during the mixing process, which initiates the material’s curing or polymerization.
The following three types of CMC sigma kneader mixers are commonly found in industrial settings:
- Non-Intermeshing Sigma Kneader Mixers: In industrial applications requiring the effective kneading and mixing of materials with complex compositions and high viscosity, the non-intermeshing design of the twin screws provides a beneficial flow pattern to enhance product quality and output.
- Intermeshing Sigma Kneader Mixers: A unique configuration of twin screws in which the screws penetrate each other offers exceptional conveying and mixing capabilities that are ideal for processing high-viscosity materials, particularly in the plastics and chemical sectors where fillers and additives must be uniformly blended.
- Sigma Blade Mixers: Sigma blade mixers are created for the uniform blending of pasty and viscous materials like dough, rubber, and heavy adhesives. Their unique design features sigma-shaped blades that efficiently fold and shear the material for comprehensive mixing. These mixers often come with a tilting function for easy discharge and cleaning, and some models may have vacuum capability to remove air from the mix and ensure a bubble-free end product.
Specifications and maintenance of CMC sigma mixer Kneader
Specifications
Volume
The volume of a sigma kneader mixer is from 0.5L to 1000L. 5L to 50L kneaders are most popular. The sigma mixer with a small volume is suitable for testing products, while the one with a large volume is for mass production.
Materials
Syndiotactic and high-impact polypropylenes, thermoplastic elastomers, polyethylene, and polyamide are some of the materials that can be kneaded by the sigma mixer. The inner kneading blades and external wall kettle often use stainless steel that meets food-grade standards.
Vacuum function
A kneader mixer can work under normal or vacuum conditions. Some materials that contain air or vapor need to be processed under vacuum. The mixer can reach a vacuum of about 0.09 to 0.1 MPa.
Temperature control
A CMC sigma mixer kneader can work at low or high temperatures. It can knead materials at a temperature of about 200°C. It can also knead materials at a temperature of -20°C. The temperature is controlled by water jackets around the kneading chamber. Liquid nitrogen can be used for low-temperature mixing.
Maintenance
Daily maintenance
Check the electrical wiring and fasteners to see if they are loose or in contact. Inspect the kneading blades, discharge gate, sealing elements, and mixing chamber for damage. Clean and lubricate the roller bearings and gear shafts. Add lubricant to the feeding part’s bearing and gearbox.
Weekly maintenance
Inspect the lubricant for roller bearings and gear shafts, and add oil if necessary. Lubricate the moving parts, including the lubricant joints and exposed parts. Check whether the gearbox is working smoothly, and add grease or sealing oil if needed.
Monthly maintenance
Inspect the motor and its drive belt. There should not be any cracks or defects in the belt, and it should be neither too tight nor too loose. Check the main components of the sigma mixer, including the bearings, sealing elements, discharge gates, and gearbox. The sealing elements in particular need to be checked for wear so that there is no leakage during operation.
Applications of CMC Sigma Kneader Mixer
Sigma kneader mixers are invaluable in industries that work with viscous or paste-like materials. Here are some applications where they are beneficial:
Food Industry
Chemical kneader mixers are perfect for mixing dough, pastes, and creams. They help develop gluten in wheat-based products, ensuring the right consistency for bread and other baked goods. Duplicates are also used to prepare candy, chocolate, and ice cream mixtures. The mixers guarantee even distribution of flavors, colors, and additives without compromising the product’s integrity.
Chemical and Plastics Industry
Chemical and plastics industries use their mixers to compound plastics, rubber, and other viscous materials to ensure thorough mixing of additives, fillers, and stabilizers in polymer processing.
Paints and Coatings
The kneader mixer can effectively disperse pigments, solvents, and additives in the formulation of paints and coatings, ensuring uniform color and consistency.
Adhesives and Sealants
In producing high-viscosity adhesives and sealants, sigma kneaders ensure even mixing and dispersion of raw materials like polymers, solvents, and fillers.
Pharmaceuticals
In the pharmaceutical industry, sigma kneader mixers are employed to blend viscous and paste-like ingredients uniformly. They mix active pharmaceutical ingredients (API), excipients, and other additives to create cohesive masses. Subsequent processing involves using kneaded material in tablet formation, capsule filling, and extraction preparation.
Cosmetics and Personal Care
Sigma kneaders help in the production of creams, lotions, and emulsions in the cosmetics industry. Sigma kneaders mix waxes, oils, pigments, and active ingredients to achieve the desired texture and performance in personal care products like moisturizers, sunscreens, and makeup.
Rubber and Elastomers
Rubber is mixed with fillers, accelerators, and other chemicals using a sigma kneader. A uniform and consistent rubber material is produced to help improve the quality of tires, seals, gaskets, and other rubber products.
How to Choose CMC Sigma Mixer Kneader
Some factors need to be considered when buying a CMC sigma kneader mixer, which may help to improve productivity and give customers durable equipment.
Industry Requirements Assessment:
When purchasing the kneader mixer, it is essential to analyze the specific needs of the industry. Some of the factors that should be assessed are material types, viscosity, batch sizes, temperature control, construction standards, and mixing intensity. Understanding the peculiarities will help businesses choose kneader mixers that perfectly fit their requirements.
Quality and Durability:
It is essential to buy a machine made with strong materials and tested for high performance. This will ensure that it stands the test of time, even with frequent use in demanding industrial environments.
Energy Efficiency:
It is advisable to go for mixers with efficient motors and well-designed mixing systems to reduce energy consumption and operating costs.
User-Friendly Controls and Monitoring:
Go for mixers with user-friendly controls and monitoring systems that allow easy operation, precise parameter setting, and real-time feedback. Kneader mixers with automated features can help streamline production processes and minimize manual intervention.
Mixing Performance:
When purchasing industrial mixers, choose those that provide uniformity and dispersion for maximum productivity. Opt for mixers with well-designed mixing elements and configurations that suit specific applications. It is also essential to consider the withdrawal facilities of kneader mixers when making a choice.
Maintenance and Service Support:
A good machine will need some level of servicing to continue to work effectively. Therefore, it is essential to consider the maintenance requirements of the CMC sigma kneader mixer and the service support available. It is best to choose a supplier that offers decent spare parts and service support to ensure that the machine will be well cared for during its lifespan.
Compliance with Safety Standards:
Ensure that the mixer being purchased adheres to safety standards and regulations. Verify that it has safety features like emergency stop buttons, protection covers, and proper grounding to safeguard operators and prevent accidents.
Return on Investment (ROI):
Consider the long-term impact of the choice kneader mixer on the business’s bottom line. Evaluate the potential return on investment (ROI) based on increased production efficiency, lower operating costs, and reduced maintenance expenses to make an economically sound decision.
CMC sigma kneader mixer FAQ
Q1: How does a CMC kneader work?
A1: The CMC kneader mixer uses a pair of top and bottom blades that create a figure-eight movement, kneading and mixing the material in the kneader.
Q2: What is the capacity of sigma mixers?
A2: The sigma mixer’s capacity varies depending on specific models, but it is generally available in different sizes. When it is between 5L and 80L, it is more likely to be used for B2B purposes. Please consult the product specifications for the capacity details.
Q3: Are sigma mixers CMC efficient?
A3: Sigma mixers are generally efficient because of the kneader’s structure and mixing principle. They can perform various operations, including mixing, kneading, and shearing, to achieve even distribution of ingredients quickly. The double-blade design of sigma kneader mixers drives the material to circulate within the mixing chamber in different directions. This leads to a repeated blending process of materials within a short time. Sigma mixers can process materials with a maximum viscosity of 3,000,000 CPS.
Q4: What are the applications of CMC sigma mixers?
A4: CMC sigma mixers can be used to produce a wide range of viscous solid and liquid materials in different industries such as food, pharmaceuticals, chemicals, plastic, and rubber. Depending on specific needs, they are often combined with other types of mixers and kneaders to achieve complete production lines.