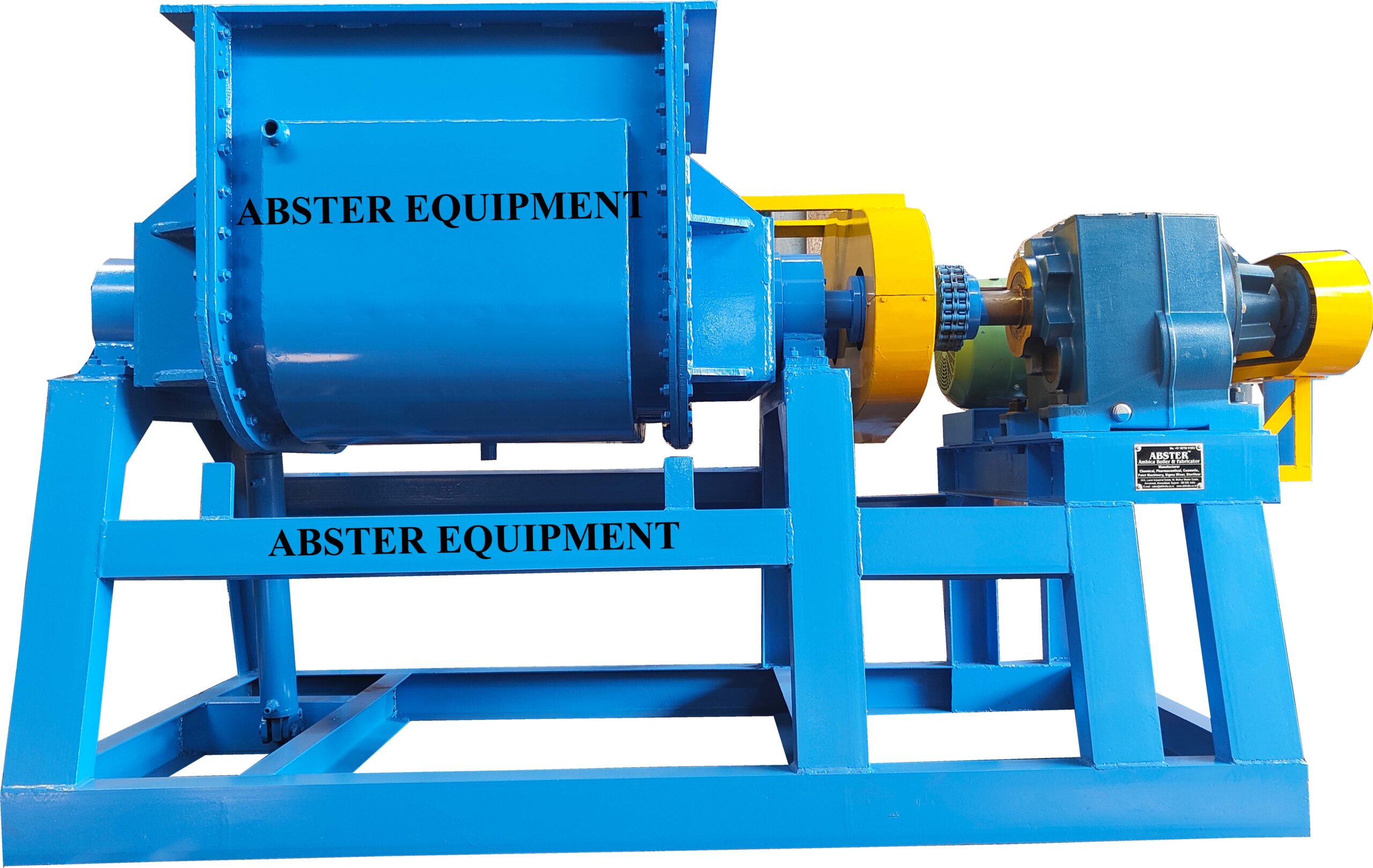
Sigma mixer extruder is used for Excellent for kneading and mixing of highly viscous materials like dough, putty, rubber solutions, adhesives, polymers etc. The mixing action is a combination of smearing, stretching, folding, dividing and recombining as the material is processed between the sigma blades and the container walls. Jacket arrangement is provided for heating or cooling application. In bigger models the container is tilted by a hydraulic cylinder to ensure complete discharge of mass. This type of mixer also available in Lab Sigma mixer extruder
Sigma Mixer Extruder
The Kneader Extruder combines the efficiency of a double arm – sigma blade mixer with the convenience of an extrusion screw for the mixing and discharging of heavy viscous materials. Such as Adhesives, Explosives, Mastics, Sealing compounds, Biscuit dough’s, Fiberglass resin dough’s, Metal powders, Silicone rubber, Butyl rubber, Food and confectionery products, Moulding preparations, Soaps and detergents, Carbon pastes, Gaskets and Gland Packing’s, Pencil erasers, Solid propellants, Ceramics Grinding wheel preparations, Pharmaceuticals, Sugar pastes, Chemicals, Hot-Melts, Plastics, Viscous rubber solutions, Chewing gum, Inks and pigment products, Putties, Crayon and pencil lead, Marzipan, Refractories.
The Sigma Mixer with Extrusion Discharge Kneader includes a set of counter-rotating kneading blades and a discharge screw. The blades are mounted on a horizontal axis in a u-shaped trough. Below the blades in a separate cavity is the discharge screw. During the mixing cycle the blades rotate toward each other while the mixing screw rotates in a reverse direction, constantly feeding new materials into the mixing blades. After the mixing/kneading cycle is complete, the screw is reversed and it transports the mixed materials from the mix zone out through a discharge die and on to further processing or packaging.
The Kneader Extruder has several advantages over conventional non-screw discharge kneaders:
- Low mixing time approx. 15% less time.
- Eliminates the manual task of scraping out sticky/tacky materials.
- Eliminates operator exposure to materials of elevated temperatures or of a toxic nature, thereby improving plant safety.
Many Different sizes and designs are available to meet the most stringent process needs. Kneader Extruders are manufactured in many sizes from 5 through 2500 Liters capacity. Other sizes manufactured on request
Working Principle of Sigma Mixer
In Sigma mixer tangential action of mixing and kneading obtained by ‘Z’ type (SIGMA) shaped kneading blades, which rotates very accurately at different speed towards each other causing product to be transferred from one end to another end. Discharge of the finished product is achieved by tilting the container or through the valves at the bottom or by means of an extrusion screw beside the container.
The mixing action is a combination of bulk movement, stretching, folding, dividing, and recombining of the material. The shearing & tearing action of the material against blades and the side walls causes size reduction of the solids. After the time period required for sterilizing the batch has elapsed, the heating circuit shuts of the pneumatics damper (exhaust) opens and cooling operation commences.
In the tangential design, the blades rotate in the trough meeting tangentially. The front blade generally rotates faster than the rear blade usually in the ratio of 3:2. Tangential blades are generally used for material of higher viscosities such as adhesives, rubber compounds, flush colors, dyes, and pigments.
In the overlapping design, the blades overlap above the saddle of the container. Due to the overlapping action, it is necessary that the relative position of the two blades is unchanged, and as a result, both the blades rotate at the same speed. Materials that flow freely or creep down into the blades are mixed using the overlapping blade action. This design offers a faster interchange of material from one blade compartment of the mixer to the other. Overlapping blade action is used for materials of lighter viscosities such as carbon pastes, clay coating, creams, and ointments. The overlapping blade produces a lower kneading and shearing compared to the tangential blade action.
Technical Specification of Sigma Mixer
Model | Capacity – Liters | Motor (H.P.) | ||
Working Capacity approx. | Gross Capacity approx. | General | Heavy Duty | |
ASM – 50 | 50 Liters | 80 Liters | 5 H.P. | 7.5 H.P. |
ASM – 75 | 75 Liters | 110 Liters | 7.5 H.P. | 10 H.P. |
ASM – 100 | 100 Liters | 150 Liters | 10 H.P. | 15 H.P. |
ASM – 150 | 150 Liters | 200 Liters | 15 H.P. | 20 H.P. |
ASM – 200 | 200 Liters | 300 Liters | 20 H.P. | 25 H.P. |
ASM – 400 | 400 Liters | 550 Liters | 30 H.P. | 40 H.P. |
ASM – 500 | 500 Liters | 750 Liters | 40 H.P. | 50 H.P. |
ASM – 750 | 750 Liters | 1150 Liters | 50 H.P. | 60 H.P. |
ASM – 1000 | 1000 Liters | 1500 Liters | 60 H.P. | 70 H.P. |
ASM – 1500 | 1500 Liters | 2100 Liters | 75 H.P. | 80 H.P. |
ASM – 2000 | 2000 Liters | 2600 Liters | 80 H.P. | 90 H.P. |
ASM – 3000 | 3000 Liters | 3800 Liters | 100 H.P. | 120 H.P. |
* Power voltage can be adjusted as per customer’s domestic power voltage requirements. * Rights of technical improvements & modification reserved. * Illustrations & dimensions are shown for information purpose only.